Location Technology Matched to the Use Case: A Customer Journey
Matching the right RTLS tag to each use case has meant supporting a variety of tag types. Wi-Fi vs ultrawideband for different accuracy levels. Outdoor tags vs indoor tags to manage finished goods. As well as tags that communicate via buttons, LEDs and buzzers. What if you could deploy a single tag that works across all of the use cases needed by the business?
As RTLS proves its value across a wider range of use cases, we share the journey of an eye glass manufacturer where a single Bluetooth® Low Energy (BLE) tag was used across several technologies including proximity, trilateration, and angle of arrival.
The production of prescription eyewear involves unique instructions for each pair of glasses. The grinding of each lens is specific to the customer as well as the design of frames. Losing an order hits profitability because of the high margin associated with custom glasses. Each pair of glasses travels through the process in a plastic bin 150cm by 250cm. Paper instructions travel with the components. The manufacturer faces several challenges. The manual process of tracking the paper traveler is prone to error and can get lost. And if the bin is removed from production for QA or rework, it can be misplaced.
To simplify management of tags, AiRISTA’s A1 tag was selected. Based on BLE technology, the A1 is low cost and remotely programmable. It provides a button for human driven workflows and a multicolored LED for alerting. The A1 also offers a variety of ways to attach.
Challenge 1: Track bins along production to less than 1 meter
The customer needed to monitor production rates in real time and locate any given order along the steps of production. Because the bins are small and travel closely along the production line, submeter accuracy was required. AiRISTA’s BLE Angle of Arrival (AoA) antennas were positioned overhead along the production line. The 5m mounting height meant the AoA antennas could be spaced 12m apart. Each A1 tag was associated with the build instructions in the manufacturing execution system (MES). As the bin entered each production cell, the assembly instructions were displayed for the associate. Note, the paper traveler was still used with each bin in case the bin was removed from production away from wireless coverage.
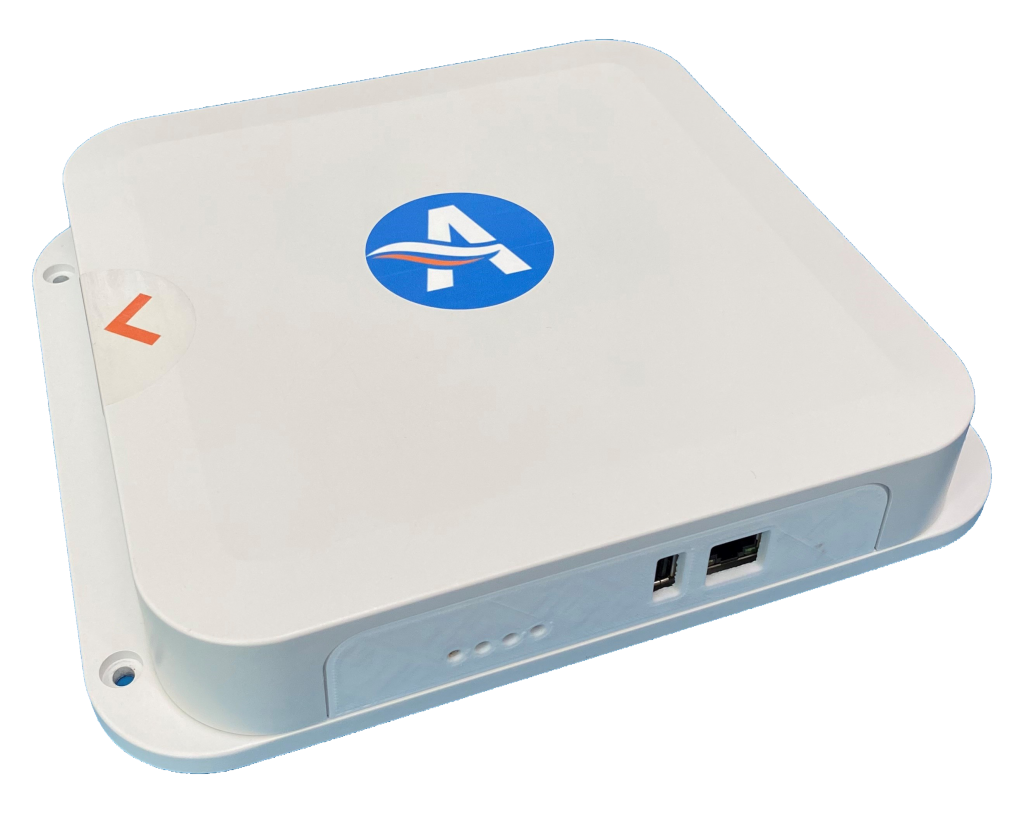
Challenge 2: Track QA and rework away from the production line
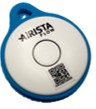
Bins removed from the production line for QA or rework could be misplaced. Locating these missing bins in real time helped ensure delivery dates and reduced waste. With a ubiquitous wireless infrastructure of access points, and access points that included internal BLE radios, the A1 tags attached to each bin could be located using trilateration to within 3 meters. In addition, the A1’s button is pushed to indicate a bin is removed from production which generates a work order in the ticket system, complete with the order ID and current location.
Challenge 3: Increase utilization of portable equipment
Tools and calibration equipment are shared among departments and can be difficult to locate in the moment. By attaching an A1 tag to these assets, the customer was able to uncover instances of hoarding, or created alerts when equipment left the production floor. Using AiRISTA’s BLE Gateway Unit (BGU) and G3 gateways at doorways and chokepoints, equipment was tracked when it moved to areas with fewer access points. Because the A1 tag includes an accelerometer, insight to utilization rates allowed better distribution of equipment where needed.
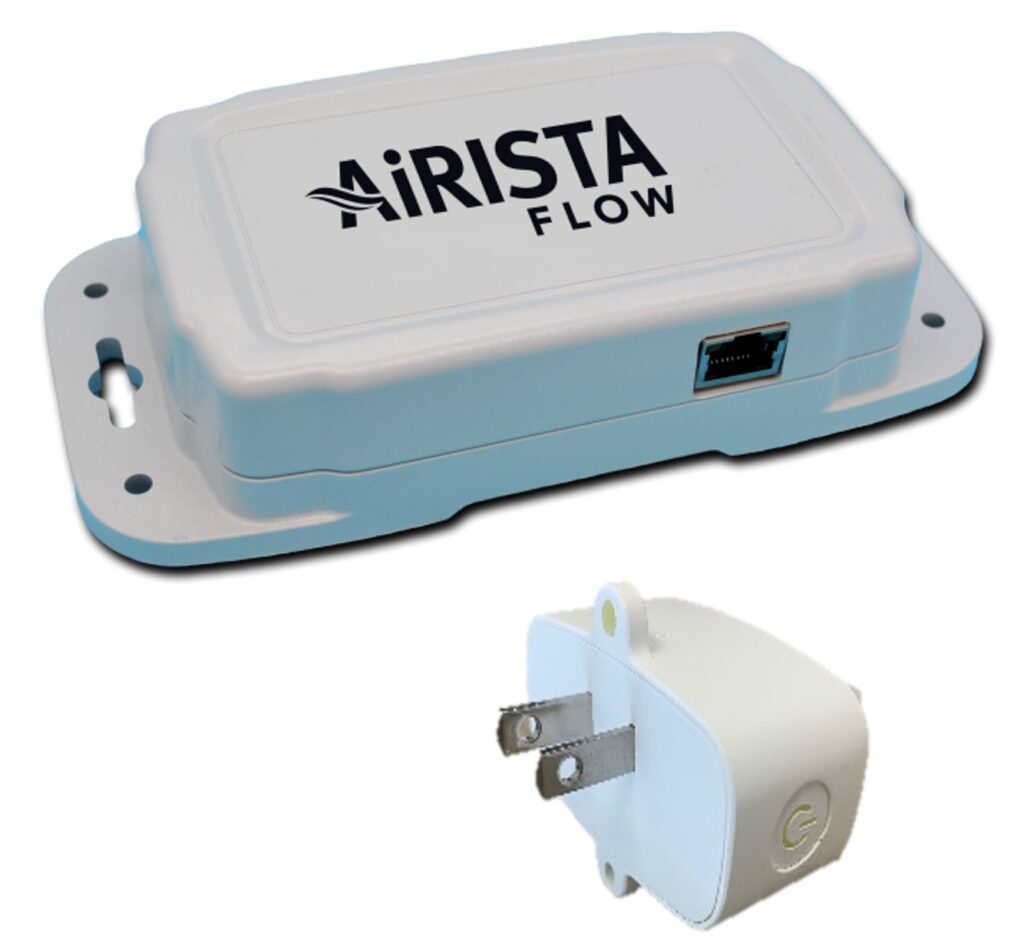
What’s Next
The success of the RTLS program has led to ideas for further process improvements. Attaching a tag to high value components in the bin will ensure the right parts as associated with each lot which will reduce rework. And AiRISTA’s next generation BLE tag will include new BLE technology with accuracy to 20-30cm opening new use cases not previously considered.
To review ways RTLS can improve your processes, please contact us at salesinfo@airista.com